AI-driven platforms have transformed wind farms into intelligent systems that predict turbine failures, optimize performance, and strategically bid energy, boosting reliability and reducing costs across operations and markets.
Read next
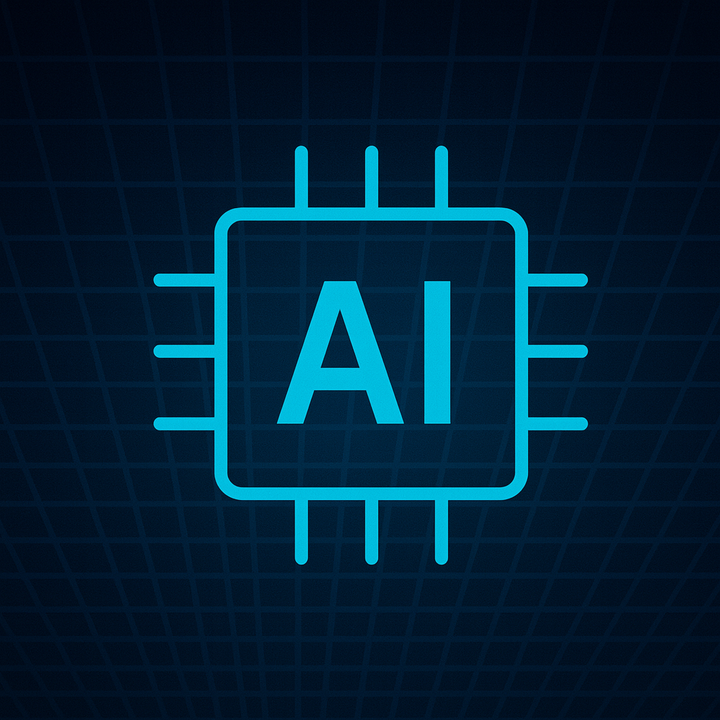
Beyond the Bubble: AI and the Future of Energy
The railroads of the 1850s, the dark fiber of the 2000s—these were not wasted dreams, but scaffolding for transformation. AI stands in that lineage. It is not a hype-train barreling toward disaster. It is the foundation of the energy future.
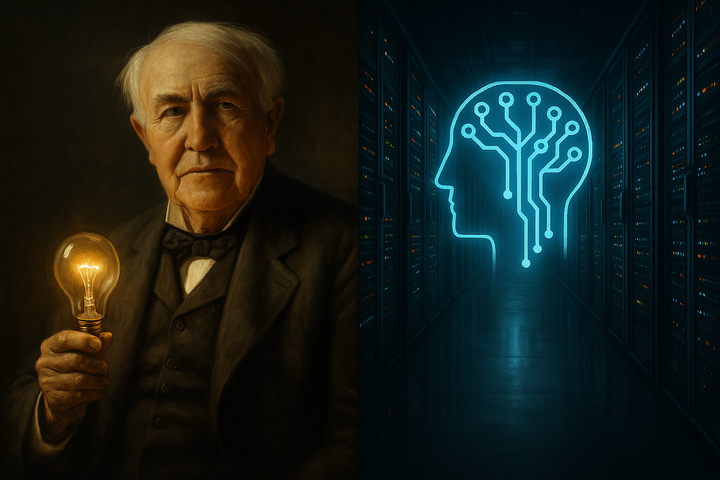
A Light in the Machine: From Edison’s Bulbs to AI’s Power Hunger
From Edison’s lightbulbs to today’s hyperscale data centers, electricity’s role has shifted from illumination to cognition. This piece explores how AI’s rapid rise is reshaping power demand, revealing how data centers can evolve from grid liabilities to assets—if policy, markets, and design align.
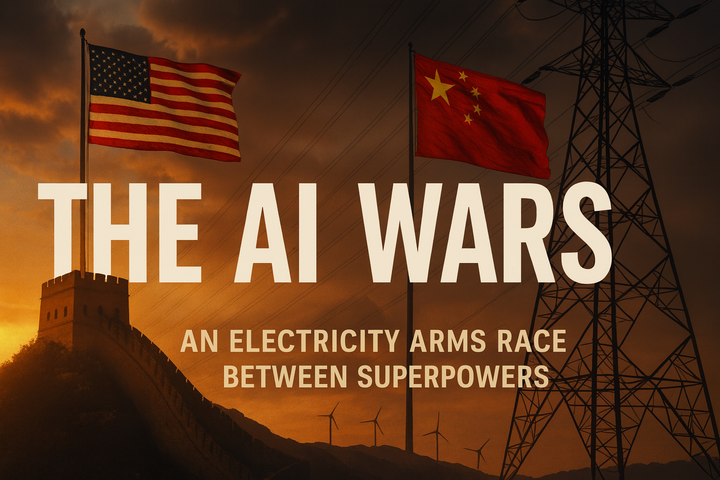
The AI Wars: An Electricity Arms Race Between Superpowers
By 2030, AI data centers could consume 945 TWh—more than Japan uses today. The U.S. faces grid strain as AI drives demand toward 50 GW by 2028, while China aligns energy, chips, and propaganda under state policy. The real AI war is over electrons, narrative, and infrastructure supremacy.